Inspection of MCA Storage Tank 2023
How do you ensure the safety and longevity of a tank storing highly corrosive chemicals? This case study explores the inspection of an MCA storage tank and the methods used to assess its condition without posing risks to people or the environment.
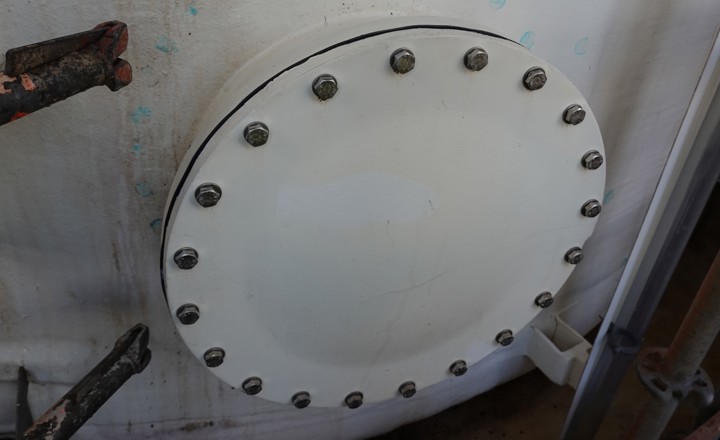
MCA Storage Tank - Case Background
Industry: Chemical Manufacturing
Project Objective: Assessment of tank condition and remaining service life
Overview: The project focused on a storage tank for monochloroacetic acid (MCA), installed in France in 2002.
Technical Details: The tank is an above-ground storage unit with a diameter of 5000 mm and a height of 8550 mm. It is constructed from glass-reinforced plastic (GRP) with a 4 mm PVC liner (thermoplastic), and built in accordance with the NF T-57900 standard.
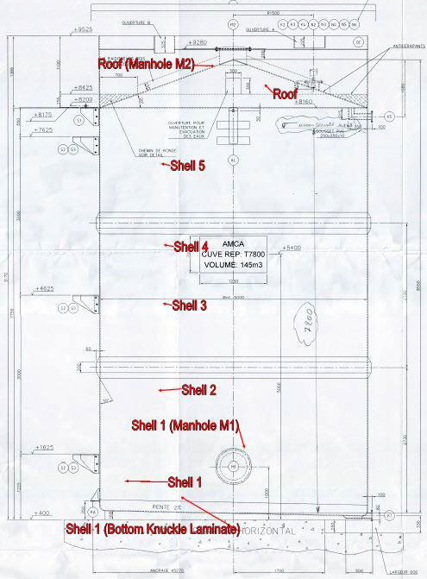
MCA Storage tank - Project Description
Problem statement: MCA is a highly hazardous and corrosive chemical, making internal inspections both risky and complex. The task was to evaluate the tank's condition while maintaining high safety and without harming the environment.
Solution: To address these challenges, we used a combination of two non-intrusive inspection methods
-
An external visual inspection of the tank’s outer surface to check for any visible signs of damage.
-
Ultrasonic testing to evaluate the internal condition of the GRP structure.
This strategy eliminated the need for confined space entry, tank emptying, or spark testing, thereby minimizing operational risks.
Results: The visual inspection revealed that the exterior of the tank was in good condition with no visible issues. The ultrasonic testing confirmed that the protective surface inside the tank was still intact, with only minor damage to the internal lining, which did not affect the tank’s functionality. The tests also indicated that the tank had several years of remaining service life.
Recommendations: Based on the findings, the following recommendations were made:
-
Conduct regular inspections, combining visual assessments and ultrasonic testing, to ensure continued safe operation.
-
Schedule the next ultrasonic test three years after the most recent inspection.
-
Integrate these inspections into the routine maintenance schedule to address potential issues early.
Conclusion: By combining visual inspection with ultrasonic testing, it was confirmed that the tank remained safe for use and did not require replacement. The total cost of the inspection was a fraction of the cost of replacing the tank, resulting in significant savings.
This inspection approach ensured ongoing operation while verifying that the tank posed no risks to safety or the environment.