Understanding the Importance of PDS in Composite Materials
In this post, we explore PDS (Polymer Damage Status), a key metric for assessing polymer condition and structural integrity over time. When working with glass fiber-reinforced plastic (GRP) equipment, understanding material longevity and performance is crucial.
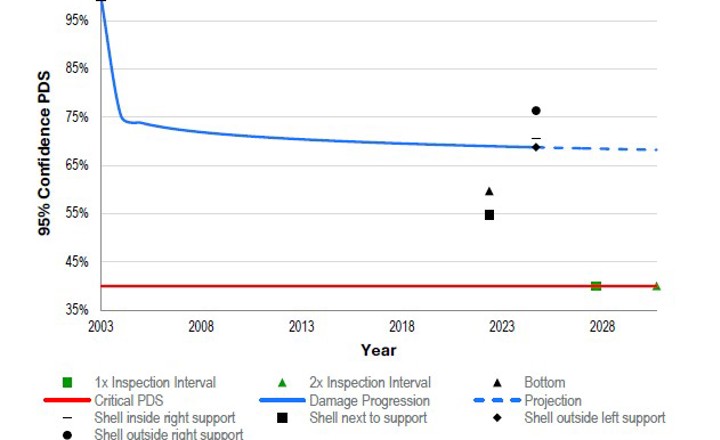
PDS in GRP Composites
What Does PDS Stand For?
In our reports, you may come across the unit PDS, which now stands for Polymer Damage Status. Previously, PDS referred to Percentage of Design Stiffness, but to better align with Fitness For Service (FFS) assessments and industry standards, it has been redefined. PDS now quantifies how much of the polymer’s original elasticity has been retained over time.
Understanding PDS
PDS is a measurement used to assess the condition of polymers and resins in glass fiber-reinforced plastic (GRP) equipment. GRP is widely used in industries such as boat building, wind turbines, storage tanks, and piping systems. When it comes to GRP, PDS expresses how much of the polymer’s flexibility remains, measured as a percentage of its original condition. If this definition seems a bit technical, think of it as a way to measure material degradation over time.
Why Is It Important to Monitor Polymer Damage Status?
The loss of flexibility in polymers and resins directly impacts the lifespan and safety of GRP equipment. Changes in PDS can lead to microcracks, which allow chemicals to penetrate the composite and reach the reinforcing glass or carbon fibers. This can compromise the structural strength of the equipment. Since polymer integrity is crucial to material durability, monitoring these changes enables early detection of degradation using ultrasonic testing and UltraAnalytix.
How Does UltraAnalytix Relate to PDS?
UltraAnalytix plays a key role in determining PDS for GRP materials by providing valuable insights into their current condition. PDS values can be calculated for the entire material thickness as well as for specific high-stress areas. With the updated terminology, PDS is now directly linked to Remaining Strength Factor (RSF), a critical concept in Fitness For Service evaluations.
PDS and Remaining Strength Factor (RSF) in Fitness For Service Evaluations
Fitness For Service (FFS) evaluations determine whether equipment can safely remain in use. In steel structures, RSF (Remaining Strength Factor) is used as an acceptance criterion, expressing the strength of damaged steel equipment compared to its original, undamaged state. The minimum allowable RSF for steel is typically 0.9 (or 90%), below which repairs or replacements are required. However, this approach does not directly translate to GRP materials. That’s why the new API 579 standard for GRP incorporates PDS as a key factor in determining RSF. By measuring PDS and GRP thickness, inspectors can now calculate RSF for GRP equipment.
New API 579 Standards for GRP
In the updated API 579 standard, the minimum allowable RSF for GRP equipment is proposed to be 0.125 (or one-eighth) in most cases. This new approach provides a clearer framework for assessing GRP condition and ensuring safety. With this shift in terminology and methodology, steel and GRP professionals can better align their understanding of Fitness For Service, making inspections and maintenance more standardized and effective.