Inspection of Nitric Acid Scrubber
In the chemical industry, equipment exposed to aggressive substances requires regular assessment to ensure safety and reliability. This case focuses on the inspection of a GRP nitric acid scrubber, installed in Belgium in 2012, to evaluate its material condition and long-term performance. With a particular focus on the corrosion barrier, an advanced inspection method was applied to assess the tank’s integrity without disrupting operations. The findings provided key insights into the scrubber’s current state and future maintenance needs. Read on to discover how this inspection was conducted and what the results revealed.
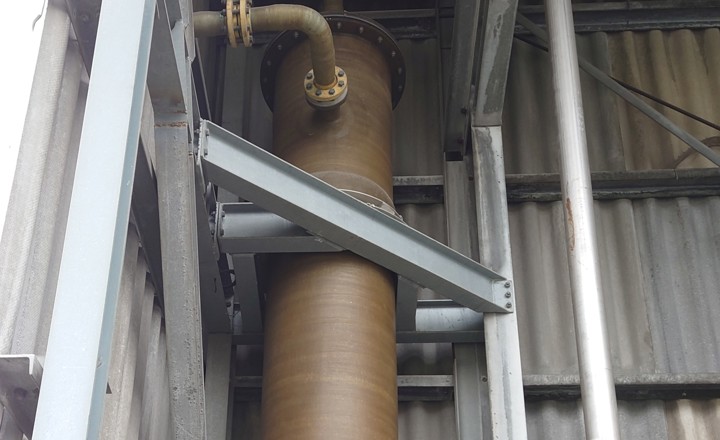
Nitric Acid Scrubber - Case Background
Industry: Chemical Industry.
Project Objective: Assessment of material condition and remaining service life.
Overview: The project involved the inspection of a GRP nitric acid scrubber, installed in Belgium in 2012.
Technical Details: The scrubber is a filament-wound Glass fiber-reinforced plastic (GRP) asset, designed to handle nitric acid (HNO₃). It has a diameter of 600 mm and a height of 4000 mm, with a protective corrosion barrier to withstand the exposure to the aggressive chemical. The unit was constructed in accordance with EN 13121 and AD2000 standards and holds a maximum operating temperature of 60°C.
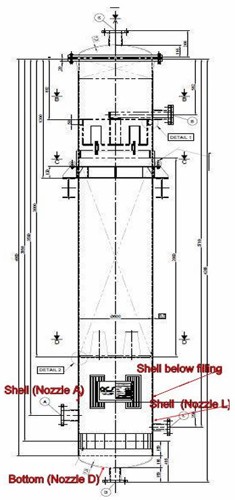
Nitric Acid Scrubber - Project Description
Problem Statement: Nitric acid (HNO3) is a highly corrosive acid that, in concentrated form, can be extremely hazardous to both humans and materials. Over time, chemical exposure can lead to degradation of the GRP material, particularly the corrosion barrier. To ensure continued safe operation, a detailed inspection of the tank’s condition was necessary to identify any potential damage without disrupting operations.
Solution:To minimize operational disturbances and ensure an accurate condition assessment, UltraAnalytix technology was utilized. The inspection included:
- Ultrasonic measurements on one section and three reinforcements
- Data validation by comparing measurements against the original specifications
- Visual assessment of the tank’s exterior and supporting structure
For safety reasons, spark testing was not conducted during the inspection to eliminate the risk of ignition.
Results:
- The corrosion barrier damage was detected beyond 80% of its original thickness in the measured section.
- No defects or damages were found on the support structure or the exterior of the tank.
- Active level controls and standard operating procedures were confirmed to be functioning correctly to prevent overfilling.
- The remaining service life of the tank was estimated to be more than six years.
The overall equipment condition was classified as “Clear,” indicating that either no damage or only minor damage was present, allowing the tank to remain in operation. The corrosion barrier was rated as “Monitor,” meaning some wear was detected, but the barrier remained functional, permitting continued use of the equipment.
Recommendations: A scheduled re-inspection using UltraAnalytix was recommended for 2023 to ensure continued optimal performance. Additionally, an inspection should be carried out after significant process changes or environmental incidents, as these factors could impact system functionality.
Conclusion: The UltraAnalytix inspection confirmed that the tank remained fit for operation without immediate repair or replacement needs. The detailed analysis allowed for early identification of wear areas and enabled the development of an optimized maintenance strategy.
By utilizing a data-driven inspection method, it was possible to extend the equipment’s service life, minimize unplanned downtime, and optimize maintenance costs.